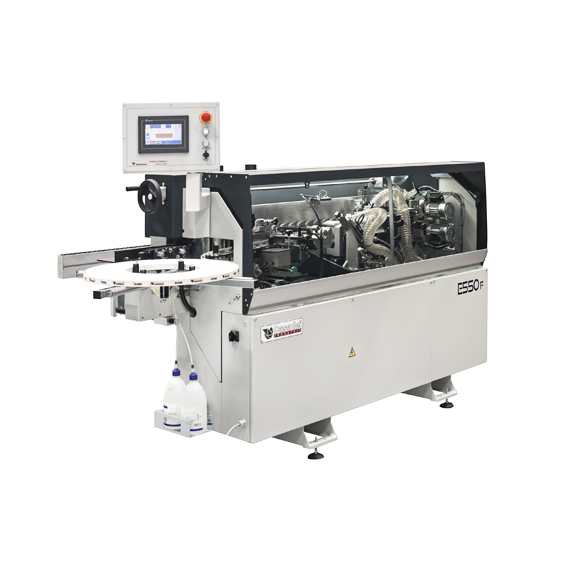
E550F
Automatic edge bander with inferior glue pot hot melt (EVA), chain panel feeding and pre-milling
Automatic edge bander with inferior glue pot hot melt (EVA), chain panel feeding and pre-milling
PERFECT GLUEING, QUICK AND PRACTICAL SET-UPS
VR2 or VS2 end trimming group to remove and mill edge excess on front/rear side of the panel
2 processing modes:
“VR2” radius (ABS and PVC thick edges)
straight (thin edges and wooden strips)
– or
“VS2” bevel (thin edges)
straight (thin edges and wooden strips)
PERFORMANCE AND VERSATILITY
TO GUARANTEE THE BEST GLUEING CONDITIONS
INSTANT PERFECT CLEANING
MIRROR FINISHING
MAXIMUM FLEXIBILITY
PERFECT PLASTIC EDGES EVEN IN BACKLIGHT
Improves the processing of large panels.
E550F/E550CRF
L 2594mm / L 3080mm